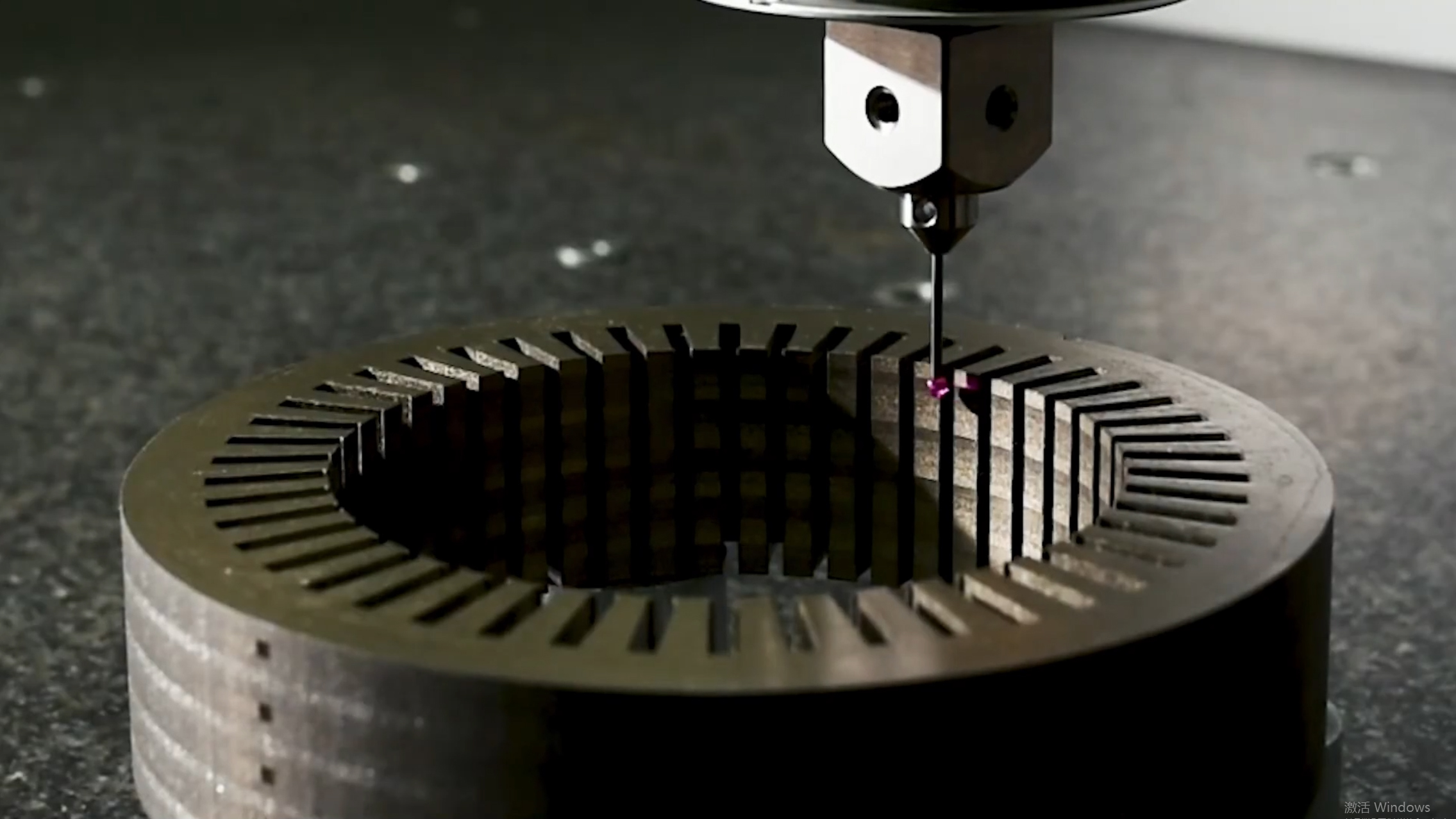
Precision Laser Cutting · Motor Laminations · Custom Thin Metal Fabrication
Powered by STIEFELMAYER effective L Laser Platform · Serving Motors, Electronics, Automotive & Precision Industries
Core Value Highlights
Experience the advantages that set us apart in the customization industry. Our commitment to innovation and precision delivers exceptional results for every project.
No Molds Needed
Skip expensive tooling costs and lengthy setup times. Our advanced manufacturing processes eliminate the need for traditional molds.
25-Day Prototype Delivery
From concept to prototype in just 25 days. Our streamlined workflow ensures rapid turnaround without compromising quality.
German Precision Equipment
State-of-the-art German machinery ensures exceptional accuracy and consistency in every manufactured component.
Supports Complex Designs
Handle intricate geometries and challenging specifications that traditional manufacturing methods cannot achieve.
Low-Volume & Custom Orders
Perfect for small batches and one-off custom projects. No minimum order quantities or setup fees required.
Trusted by Industry Leaders
Join thousands of satisfied customers who rely on our precision and expertise
Processable Product Types
Advanced laser cutting solutions for precision metal processing across multiple industries.
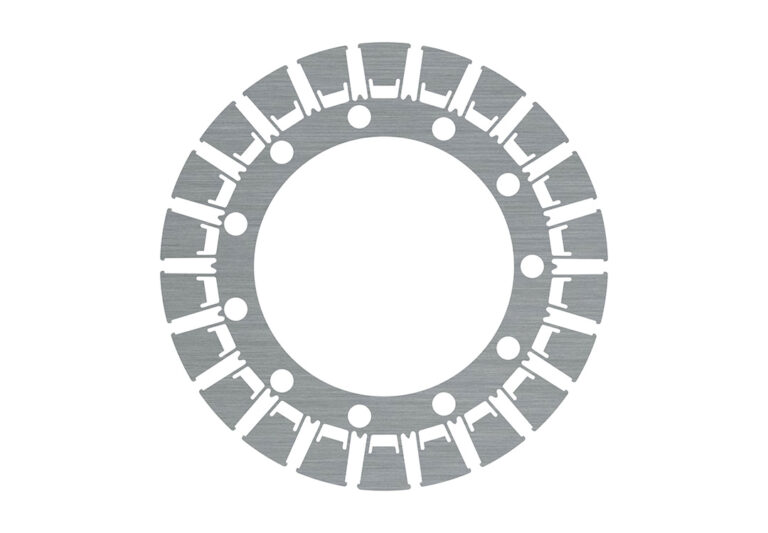
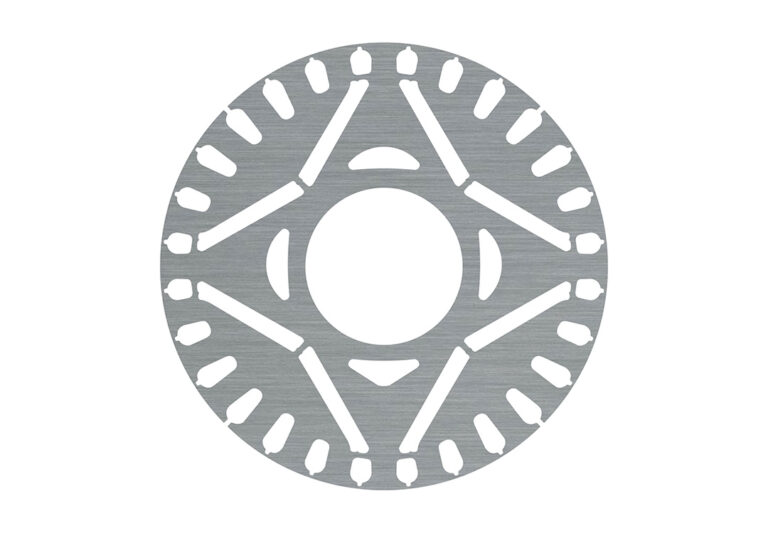

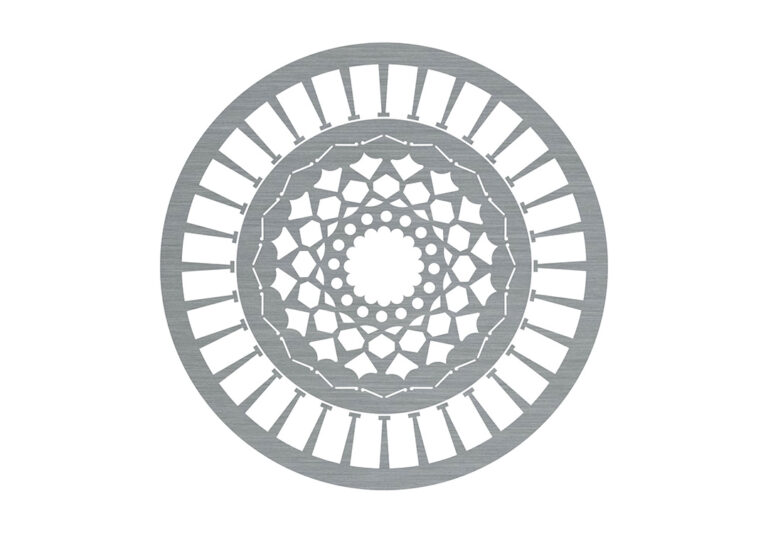
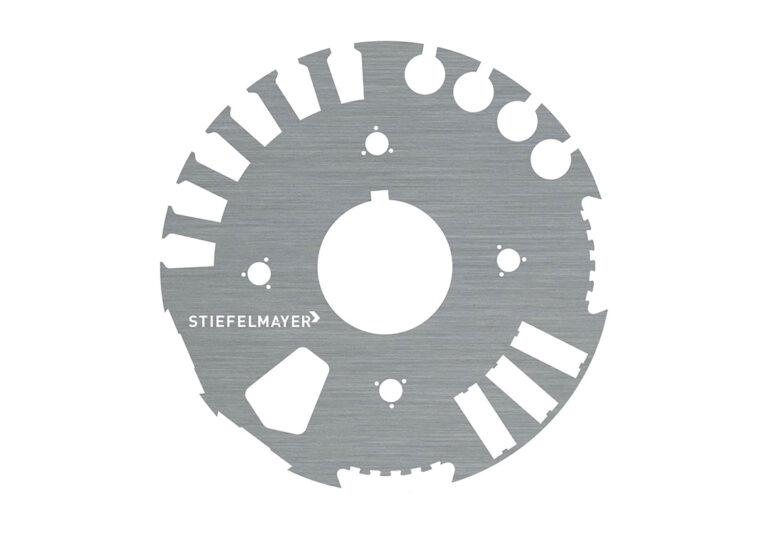
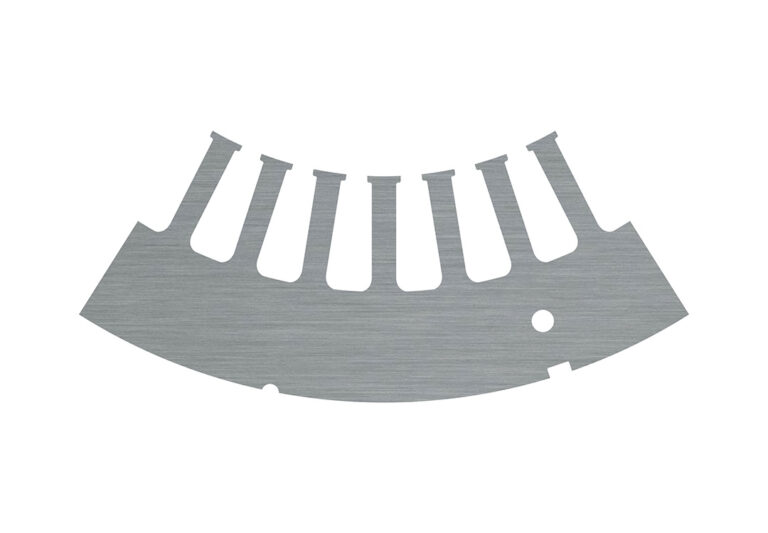
What We Offer
LS specializes in laser-cut stator and rotor laminations for R&D and small-batch production. Our precision manufacturing solutions deliver exceptional quality for your electrical motor development needs.
Stator Laminations Prototyping
High-precision laser-cut stator laminations designed for optimal magnetic performance. Perfect for motor development and testing phases with rapid turnaround times.
Rotor Laminations Prototyping
Precision-engineered rotor laminations with complex geometries and magnetic optimization. Ideal for permanent magnet and induction motor applications.
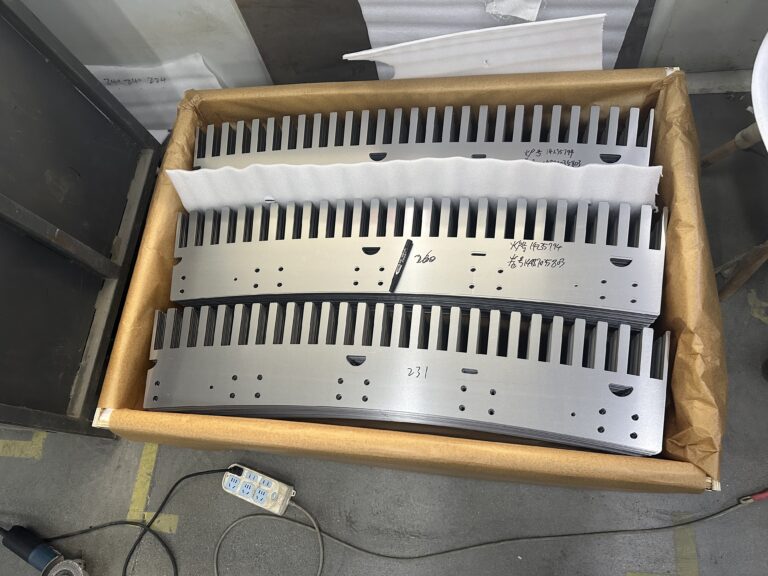
Custom Small-Batch Manufacturing
Flexible production runs from single prototypes to small series manufacturing. Cost-effective solutions without minimum order requirements.
Ready to Start Your Project?
Discover how our specialized lamination services can accelerate your motor development and production goals.
From Drawing to Delivery
Our streamlined 5-step process ensures precision, quality, and timely delivery for every project from concept to completion.
Submit Drawings
Submit your technical drawings and communicate your specific requirements with our team.
Engineering Assessment
Our engineers evaluate your project and provide professional technical consultation.
Sampling & Quotation
Receive detailed quotations and sample prototypes for your approval and testing.
Production Processing
Advanced manufacturing using our high-precision laser equipment and German engineering.
Quality Control & Delivery
Rigorous quality inspection followed by secure packaging and timely delivery.
Have Questions?
Get instant answers to common questions about our services, processes, and capabilities through our comprehensive FAQ section.
Why Engineers Trust LS
Our advanced laser cutting technology and precision engineering deliver superior results for motor lamination prototyping and small-batch production.
Laser Cutting vs Traditional Stamping
No tooling required, immediate production start, and complex geometries achievable without additional costs.
- • No tooling costs
- • Instant design changes
- • Complex shapes
- • High tooling investment
- • 25+ day lead time
- • Limited complexity
Unmatched Efficiency
25-day complete prototype delivery with simultaneous speed and accuracy optimization.
Precision Engineering
German-engineered equipment ensures consistent quality and tight tolerances for critical applications.
Complete Customization
From single prototypes to small batch production, we adapt to your specific requirements without minimum order constraints.
German Precision Technology
Powered by Stiefelmayer Effectie L laser cutting systems
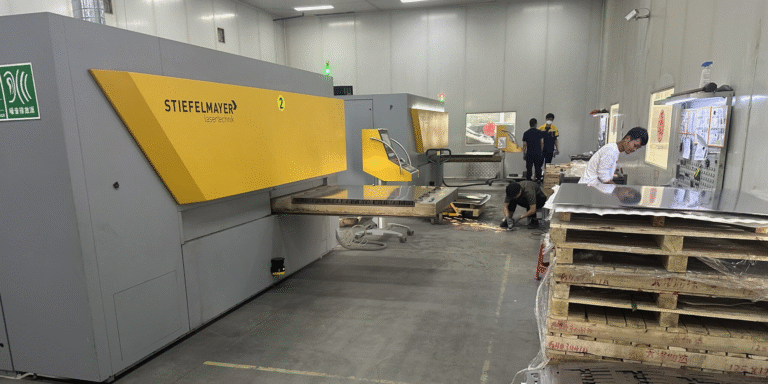
Technical Specifications
Manufacturing Advantages
Experience the LS Advantage
Discover how our German precision technology and engineering expertise can transform your motor development process.
Who We Help
From R&D engineers to international buyers, we serve diverse industries with precision laser cutting solutions for motor lamination prototyping and small-batch production.
Motor R&D Engineers
Pain Point:
Long lead times for prototype tooling delay design validation and slow down product development cycles.
LS Solution:
Direct laser cutting from CAD files eliminates tooling wait time, enabling rapid design iterations and faster validation cycles.
Stamping & OEM Partners
Pain Point:
High upfront tooling costs and long setup times create barriers for prototype validation and small batch orders.
LS Solution:
Complement stamping operations with tooling-free laser cutting for prototypes and bridge production before full-scale manufacturing.
Research Institutions
Pain Point:
Limited budgets and need for precise, small-quantity samples for experimental research and academic studies.
LS Solution:
High-precision single pieces or small batches at competitive prices, supporting research with exact specifications and tight tolerances.
Electric Motor Startups
Pain Point:
Limited capital for tooling investment and need for rapid iteration during product development and market validation phases.
LS Solution:
Zero tooling investment enables fast, cost-effective prototyping and small production runs for market testing and investor demonstrations.
International Buyers
Pain Point:
Need reliable overseas suppliers with consistent quality, competitive pricing, and responsive communication across time zones.
LS Solution:
Proven track record serving US, Australia, Thailand, Korea, and Germany with ISO-certified quality and English-speaking support.
Our Impact
Ready to Accelerate Your Project?
Join engineers and companies worldwide who trust LS for their motor lamination prototyping needs. Get your custom quote today.
Performance Metrics & Customer Testimonials
Our commitment to excellence is reflected in our performance data and trusted by industry leaders worldwide.
99.8%
On-Time Delivery Rate
99.9%
Quality Pass Rate
15+
Years of Industry Experience
500+
Global Clients Served
What Our Clients Say
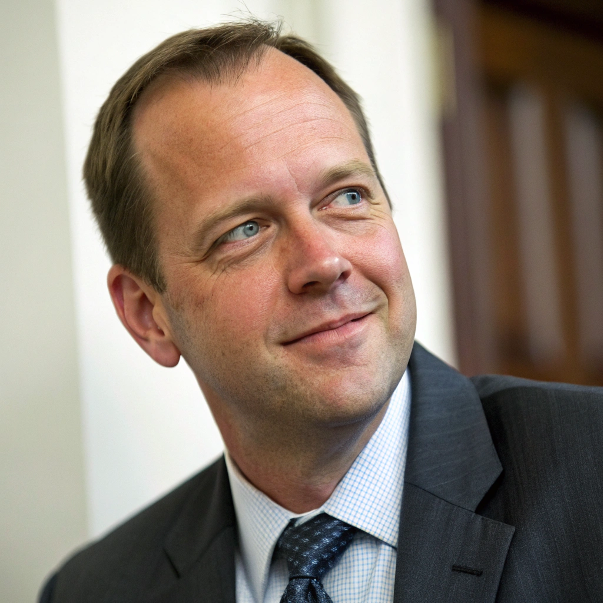
Sarah Johnson
Chief Operations Officer, EV Motors Inc.
"Their stator and rotor laminations have consistently exceeded our quality expectations. The precision and reliability of their manufacturing process have significantly improved our motor efficiency. Their team's responsiveness and technical expertise make them an invaluable partner."
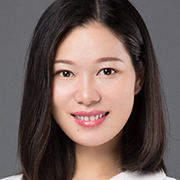
Michael Chen
Procurement Director, Global Electric Solutions
"We've partnered with them for over 5 years, and their ability to scale production while maintaining exceptional quality has been crucial to our growth. Their prototype-to-mass production timeline is unmatched in the industry, giving us a competitive edge in bringing new products to market."

Emma Rodriguez
Engineering Manager, Advanced Motor Technologies
"Their technical expertise in stator and rotor laminations has helped us solve complex engineering challenges. The consistency in their manufacturing process ensures that every batch meets our strict specifications. Their collaborative approach makes them feel like an extension of our engineering team."
Latest Blog Insights
Explore our most recent insights on laser cutting, materials, and manufacturing trends.
Laser Cutting Basics
A guide for beginners to understand core laser cutting concepts and methods.
Material Selection Tips
Learn how to choose the right materials for laser cutting efficiency and performance.
2024 Industry Trends
Discover what's shaping the future of laser cutting and manufacturing sectors.
Laser Optimization Tips
Tips for fine-tuning laser parameters to cut different materials effectively.