LS Lamination — Precision Laser-Cut Laminations Since 2010
From 24 h Prototype to 3 M+ Mass Production, Trusted in 5 Continents
Scroll Down
Our Brand Story
Founded in 2010 by Anthea Chen, LS Lamination was born from a vision to revolutionize the electric motor industry with precision-engineered laminations. What began as a small workshop with a single laser cutting machine has evolved into a global leader in high-precision lamination solutions.
CEO Laser beam recognized the growing demand for high-quality, custom laminations that could meet the exacting standards of next-generation electric motors. Drawing from her background in electrical engineering and manufacturing, she established LS Lamination with a commitment to quality, innovation, and customer satisfaction.
Our Core Values
-
Integrity
We honor our commitments and operate with transparency.
-
Innovation
We continuously improve our processes and solutions.
-
Craftsmanship
We take pride in precision and attention to detail.
-
Sustainability
We commit to environmentally responsible practices.
Our Mission & Vision
Empower next-generation electric motion with high-precision laminations that drive efficiency, performance, and innovation.
We are committed to providing our customers with the highest quality lamination solutions that meet their exact specifications, delivered on time and with exceptional service. By focusing on precision engineering and continuous improvement, we enable our clients to push the boundaries of what's possible in electric motor technology.
How We Fulfill Our Mission:
- Investing in cutting-edge laser technology
- Maintaining rigorous quality control standards
- Providing rapid prototyping and scaling capabilities
- Offering comprehensive technical support
Be the global benchmark for prototype-to-mass lamination solutions, recognized for excellence in every aspect of our business.
We aspire to be the partner of choice for companies developing the next generation of electric motors and transformers. Our vision is to set the industry standard for quality, innovation, and customer satisfaction, while expanding our global footprint to serve clients across all continents.
Our Vision Targets:
- Establish manufacturing facilities on all major continents by 2030
- Achieve carbon neutrality in our operations by 2035
- Develop proprietary lamination technologies that set new industry standards
- Build a diverse, skilled workforce that drives innovation
Integrity · Innovation · Craftsmanship · Sustainability
These core values guide every decision we make and every action we take. They are the foundation of our company culture and the principles that define who we are as an organization.
Integrity
We maintain the highest ethical standards in all our business dealings. We are honest, transparent, and accountable in everything we do, building trust with our customers, suppliers, and employees.
Innovation
We embrace change and continuously seek better ways to serve our customers. We invest in research and development to stay at the forefront of lamination technology and manufacturing processes.
Craftsmanship
We take pride in our work and are committed to excellence in every detail. Our team of skilled professionals brings precision, care, and expertise to every project, ensuring the highest quality outcomes.
Sustainability
We recognize our responsibility to the environment and future generations. We strive to minimize waste, reduce energy consumption, and implement eco-friendly practices throughout our operations.
Timeline
Discover the key milestones in LS Lamination's journey of innovation and growth.
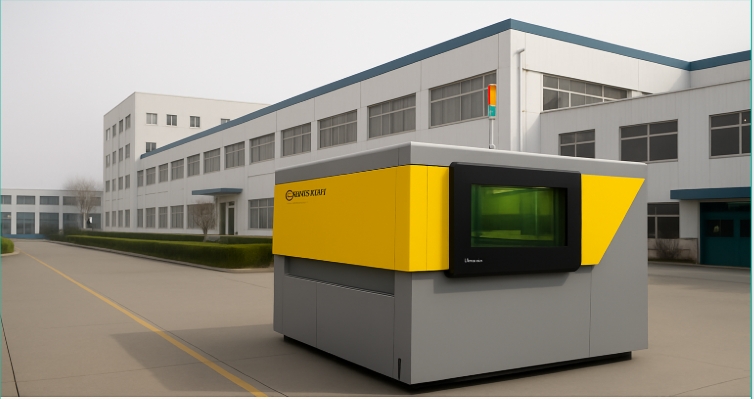
Founded in Suzhou
LS Lamination was established in Suzhou, marking the beginning of our journey. Our first laser cutting machine for laminations was put into operation, setting the foundation for our precision manufacturing capabilities.
Automation & Certification
Our first automated bonding production line was put into operation, significantly enhancing our manufacturing efficiency. We also achieved ISO 9001 certification.
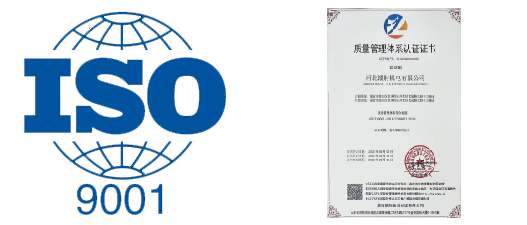
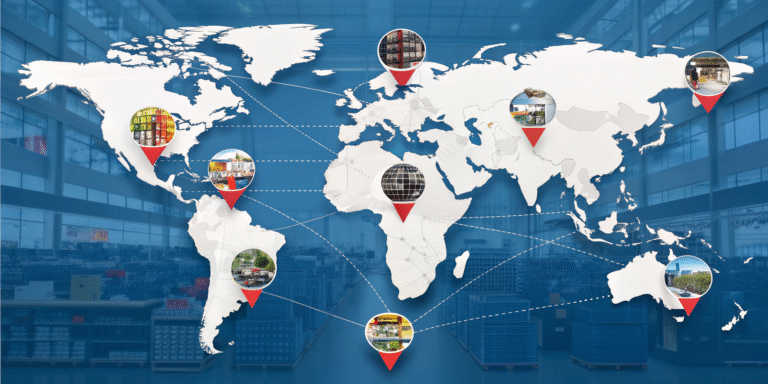
Global Expansion
Our exports surpassed 1 million sets, a significant milestone in our growth. We expanded our services to over 20 countries worldwide, including the USA, Australia, Thailand, South Korea, and Germany, establishing LS as a global supplier of high-quality laminations.
Advanced Technology
We introduced the German Stiefelmayer Effectie L laser cutting machine, significantly enhancing our precision manufacturing capabilities. We also established a 24-hour prototyping system, allowing us to provide rapid turnaround times for our customers' development projects.
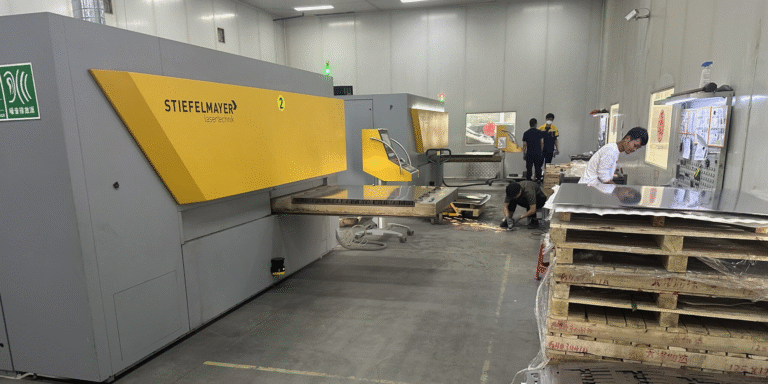
Founded in Suzhou
First laser cutting machine for laminations put into operation.
Automation & Certification
Automated bonding line & IATF 16949 certification.
Global Expansion
Exports surpassed 1M sets, serving 20+ countries.
Advanced Technology
German Stiefelmayer Effectie L & 24h prototyping system.
Aerospace & Defense Ready
AS9100D audit & ITAR-ready secure workshop.
Showcase
Experience our advanced manufacturing capabilities and precision engineering excellence.
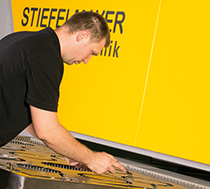
Laser Cutting
Precision cutting with German Stiefelmayer technology
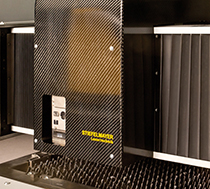
Automated Adhesive Application
Precise bonding for optimal lamination integrity
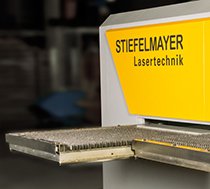
Vacuum Heat Treatment
Controlled thermal processing for optimal material properties
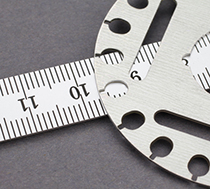
CMM Inspection
High-precision coordinate measuring for quality assurance
30 µm
Laser Beam Spot Size
Ultra-precise cutting for complex geometries and fine details
3 Million Sets
Annual Production Capacity
Scalable manufacturing to meet high-volume demands
Fe-Co ≤ 0.05 mm
Minimum Material Thickness
Specialized processing for ultra-thin iron-cobalt alloys
Quality System & Certification
Our commitment to quality is backed by international certifications and rigorous quality control systems.
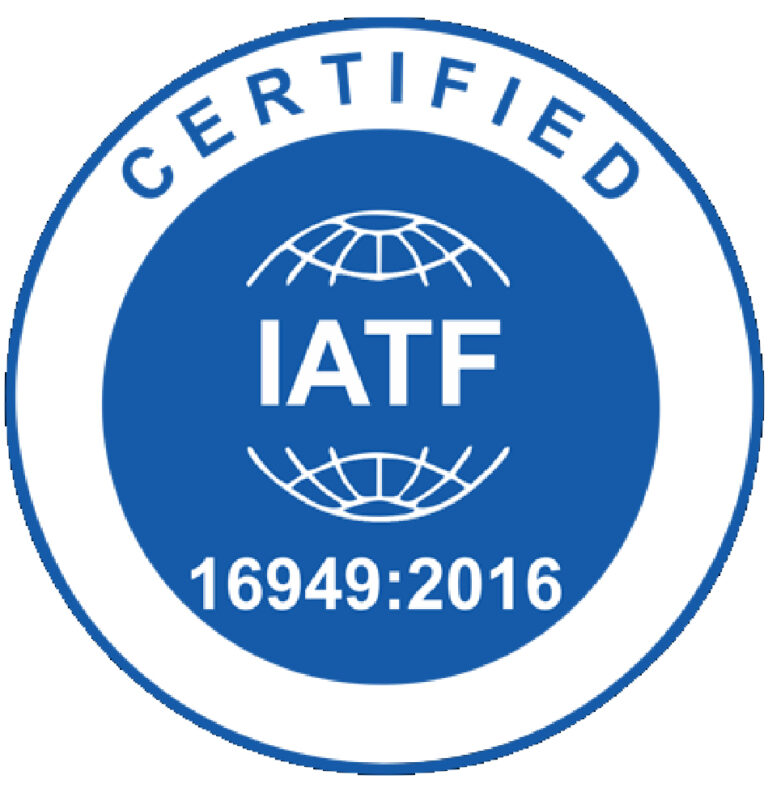
IATF 16949
Automotive Quality Management
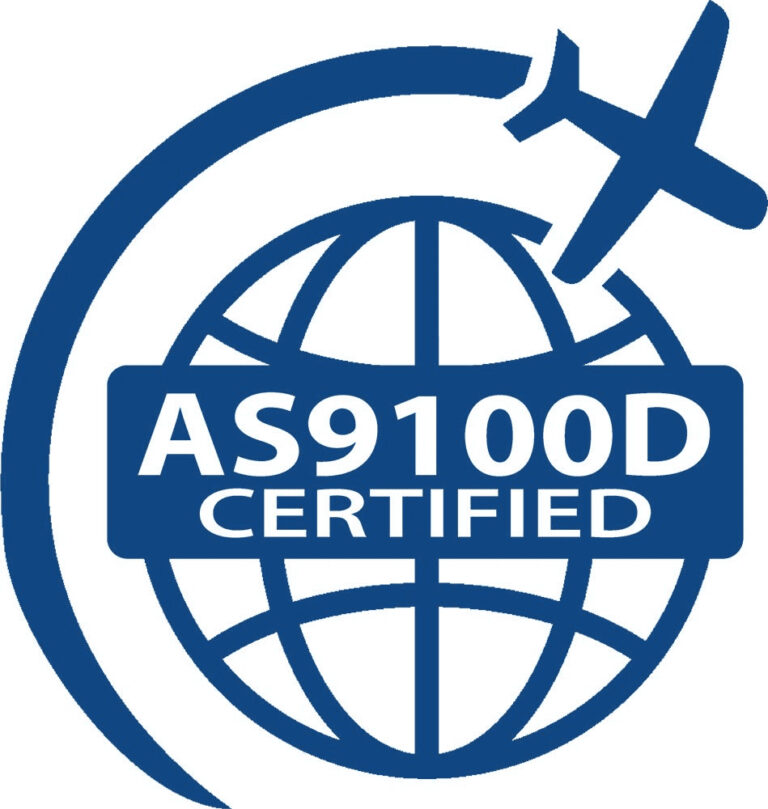
AS9100D
Aerospace Quality Standard
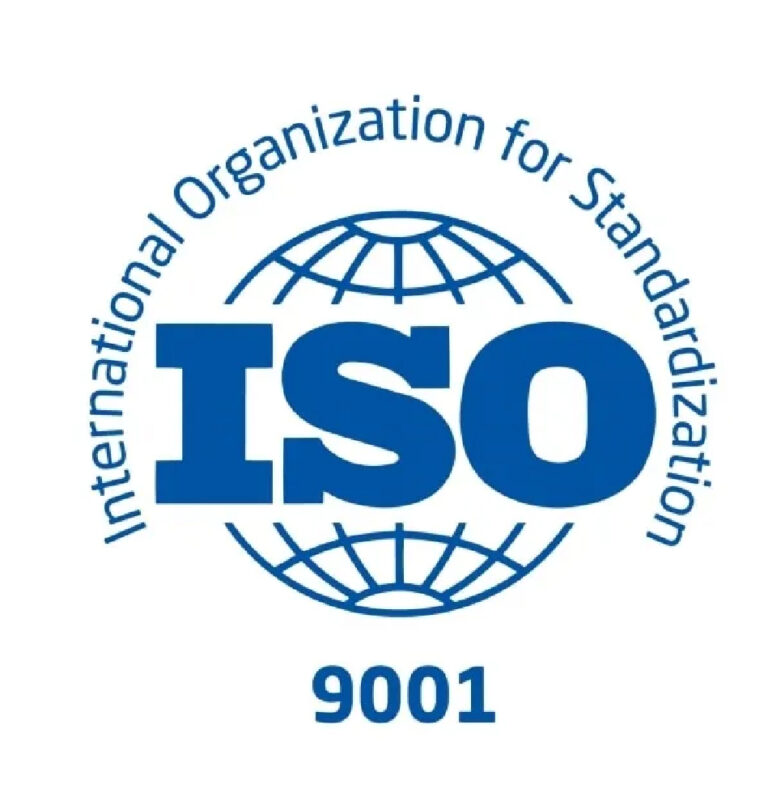
ISO 9001
Quality Management System
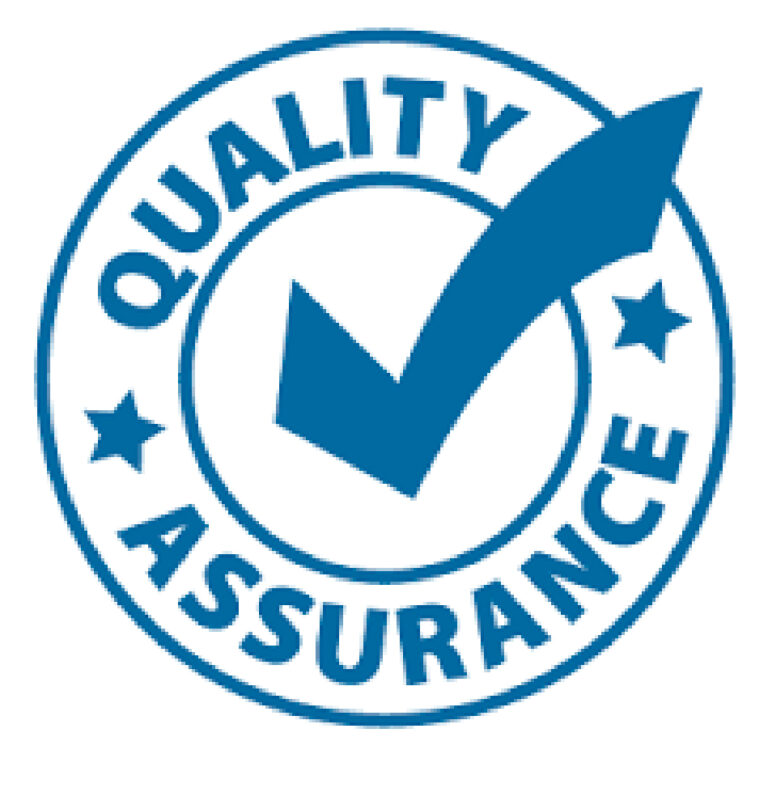
Quality Assurance
Internal Quality Standards
Barcode Traceability System
Our comprehensive traceability system ensures every component can be tracked throughout the entire production process, from raw material to finished product.
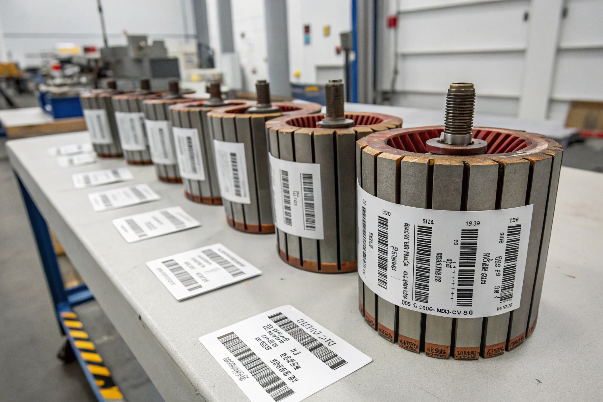
Each lamination is assigned a unique barcode for complete production history tracking and quality assurance.
Quality Assurance FAQ
How do you handle PPAP requirements?
We provide comprehensive Production Part Approval Process (PPAP) documentation to meet automotive and aerospace industry standards. Our PPAP packages typically include:
- Design records and engineering change documents
- Process flow diagrams and FMEA
- Control plans and measurement system analysis
- Initial sample inspection reports with dimensional results
- Material and performance test results
We can customize PPAP documentation levels (1-5) according to your specific requirements.
Can you provide COC/CMM documentation?
Yes, we provide both Certificate of Conformance (COC) and Coordinate Measuring Machine (CMM) reports:
- COC: Our certificates verify that materials and manufacturing processes conform to all specified requirements and standards.
- CMM Reports: We utilize high-precision coordinate measuring machines to verify critical dimensions and provide detailed measurement reports with each shipment.
All documentation is available in digital format and can be customized to meet your specific quality assurance requirements.
How do you manage FOD control?
Our Foreign Object Debris (FOD) control program is particularly important for aerospace and defense applications. Our comprehensive approach includes:
- Dedicated clean manufacturing areas with controlled access
- Regular FOD awareness training for all production personnel
- Tool accountability and control procedures
- Regular FOD inspections and audits throughout the production process
- Special packaging protocols to prevent contamination during shipping
We maintain detailed FOD prevention records and can provide documentation of our control measures upon request.
Material Utilization
At LS Lamination, we're committed to sustainable manufacturing practices that maximize material utilization and minimize environmental impact.
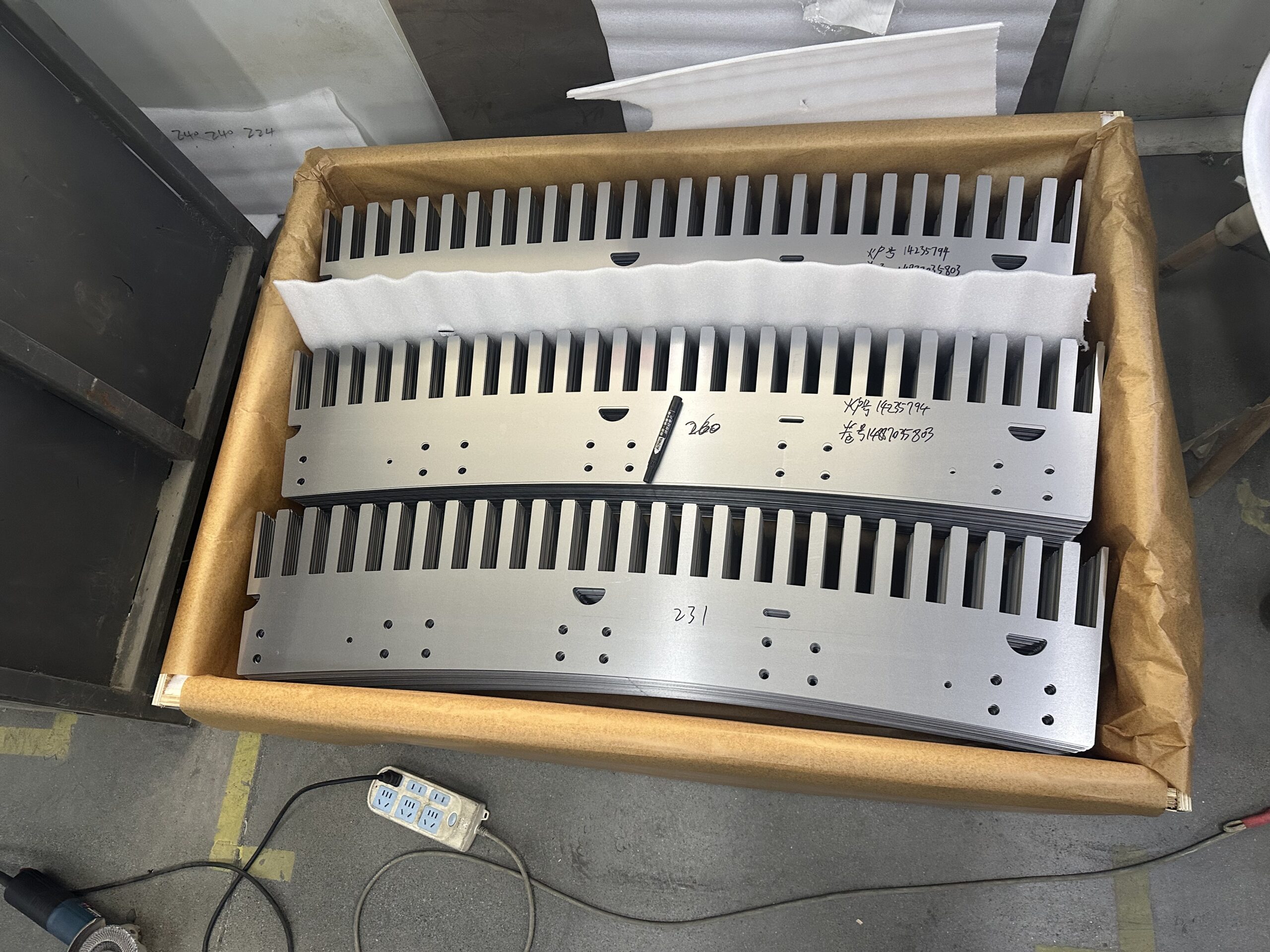
Sustainability Through Innovation
Our advanced laser cutting technology represents a significant leap forward in sustainable manufacturing for stator and rotor laminations. By optimizing material usage and reducing energy consumption, we're setting new industry standards for eco-friendly production.
Average material utilization rate, significantly higher than industry standard
Scrap material recycling in our closed-loop system
Energy reduction compared to traditional stamping methods
Energy Efficiency Comparison
Our Stiefelmayer Effectie L laser cutting machines from Germany deliver precision with significantly lower energy consumption compared to traditional stamping methods.
Energy Reduction
Lower power consumption compared to traditional stamping
Material Efficiency
Optimized nesting algorithms maximize material usage
Recycling Rate
Complete recovery of all scrap material
Our sustainable manufacturing approach not only reduces environmental impact but also translates to cost savings for our customers. By maximizing material utilization and minimizing waste, we can offer competitive pricing while maintaining the highest quality standards.
Customer Success
Our partnerships with industry leaders have resulted in exceptional outcomes. Here's what our clients have to say about working with LS Lamination.
14 days to complete road test samples - the fastest turnaround we've experienced with any supplier. LS Lamination's precision and efficiency have become essential to our development cycle.
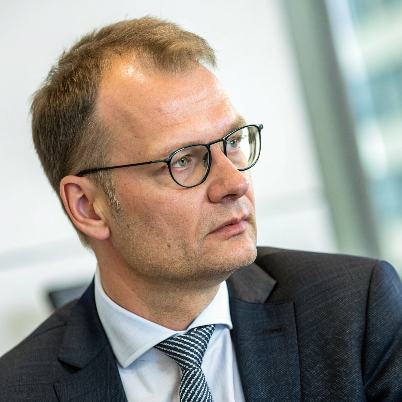
Bosch E-Drive Chief Engineer
Electric Vehicle Division
The Fe-Co lamination performance exceeded our predictions by 5%. This improvement directly translated to extended flight time for our eVTOL prototype, a critical advantage in our development phase.
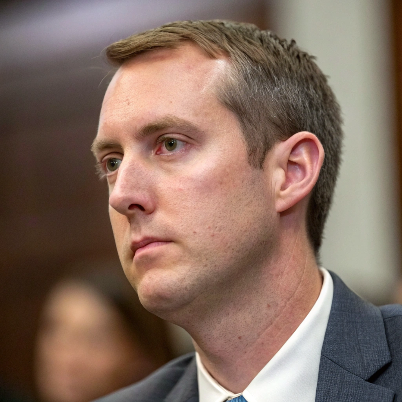
GE Aviation eVTOL Project Manager
Advanced Air Mobility
Trusted by Industry Leaders
LS Lamination has successfully delivered over 500 custom projects for clients across automotive, aerospace, and energy sectors. Our commitment to precision, quality, and rapid turnaround continues to set new industry standards.
Ready to Boost Your Motor Efficiency?
Upload your drawings & get a quotation in 24 h.